Sawmills are ever-so-important in the wood processing industry. This Sawmill guide will answer exactly what is a sawmill, how do sawmills work, and the different types of sawmill available.
Table of Contents
- What Is a Sawmill?
- What Do Sawmills Produce?
- Types of Sawmill
- How Are Sawmills Powered?
- How Does a Sawmill Work? The Process Lumber Milling
- How to Choose a Sawmill
- How to Use a Sawmill
- Tips for Efficient Sawmill Use
- FAQs (Frequently Asked Questions)
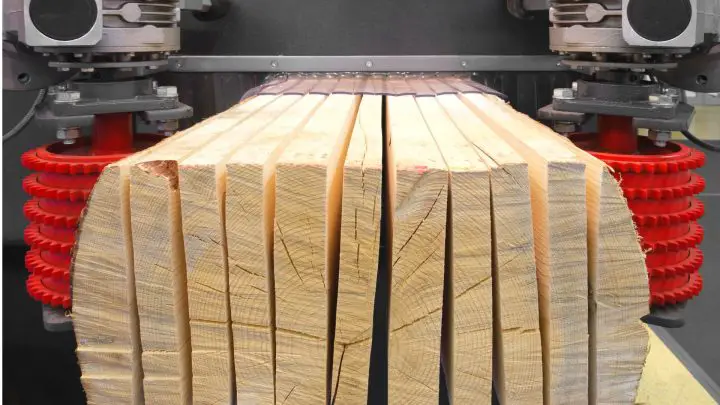
What Is a Sawmill?
A sawmill is a specific cutting or sawing machinery that turns round logs into rectangular timbers ready for use in manufacturing. However, the term sawmill could also refer to another different concept within the industry, the location where people mill lumber.
The sawmill is described as all the land on which the sawmill sits. This includes the log-sorting yard, all the milling machinery, and the storage area for wooden planks.
You may or may not already have heard the term head rig, which is the technical name for the core sawing machine in the sawmill industry, but an extensive support structure is crucial for the head rig to function correctly. Therefore, a sawmill can be most accurately described as the entire system that turns logs into lumber.
Most modern sawmills are highly productive and enormous commercial enterprises. Some of these locations dotted around will employ hundreds of workers and have shift patterns around the clock to keep lumber production constant and efficient.
Sawmill Invention
So, what led to the invention of the sawmill?
Prior to this, people cut and split wooden boards manually using hand tools. After that, people used a whipsaw which is a long blade that cut logs and requires manual pulling. As you can imagine, the process was extremely tedious and tiring, hence, the need for innovation and the sawmill.
The history of sawmills dates as far back as the Roman empire. The Hierapolis sawmill is the name of the first known sawmill, created somewhere within the third century A.D. We know this because archaeologists examined the sarcophagus of a miller in modern-day Turkey, what used to be known as Asia Minor, where they discovered a waterwheel with a crank slider mechanism and two saws cutting through blocks.
This Roman waterwheel-powered saw was a historic advancement in both engineering and production. Water-powered stone sawmills could be found throughout the Byzantine Empire in the 6th century, and by the 11th century, they had spread from Spain and North Africa to Central Asia.
So, who invented the sawmill? The design of the sawmill practically remained the same until the circular saw blade was invented during the Industrial Revolution. Samuel Miller gets credit from historians and was awarded a British patent for the blade in 1777. However, others claim the Dutch developed it in the 17th century or that it was the American Shaker Sister Tabitha Babbitt.
Regardless of who invented it, the saw wasn’t used much until the middle of the 19th century due to its high price and inferior blades. The majority of sawmills today use industrial-sized band saws.
What Do Sawmills Produce?
Sawmills are capable of producing high amounts of all kinds of lumber, although most will specialize in producing a specific type of lumber. Sawmills in North America process either softwood or hardwood trees.
Softwood trees are evergreen species with permanently attached needles. They include cedar, pine, spruce, hemlock, fir, and redwood. In contrast, hardwood trees are deciduous species that shed their leaves in autumn before producing new ones in spring. They include walnut, maple, beech, cherry, elm, and oak.
These two species require different machines and tools in order to process them. Some sawmills may purchase the equipment to process both types of trees but this isn’t so common.
You will find softwood materials being used in light commercial construction industries for rough carpentry and building framing. While hardwood lumber will be found in residential construction for finished products like furniture, flooring, staircases, and plywood panels.
Most sawmills make three main products on their production line:
- Timbers
- Dimensional lumber
- Board
Timbers
Timbers are large-cut posts used within the construction industry. They typically have a thickness of over 5 inches and provide essential structural support. Timbers are used as beams or posts by construction companies when building projects like houses or barns.
Dimensional Lumber
Dimensional lumber is the most common product in a sawmill production line, used in construction and manufacturing applications for joists, headers, plates, studs, and rafters. These lumber planks are generally smaller than timbers and are measured according to standardized sizes, but can also be planed to specific smoothness. Some standard sizes are:
- 2x4s
- 4x4s
Dimensional lumber can be anywhere between 2-5 inches thick and 2-12 inches wide. Their sizing can be somewhat difficult, as their size is reduced slightly after planing. A roughly cut plank exiting the sawmill head rig is 2 inches thick and 4 inches wide (2×4). However, the precise dimensions of this 2×4 exiting the sawmill’s planer are 1 ½ inch thick by 3 ½ inches wide.
Board
Last but not least are thin planks called “board” that typically measure between ¾ of an inch to 1 inch thick. Boards are used to form sheathing structures, plank floors, and frames for furniture, ranging from 2-12 inches wide. Rough-cut boards are what you’ll see being used regularly for pallets and crates.
Wooden planks can also be made into specialized shapes and contours by sawmills for decoration and architecture purposes. Sawmills are able to produce a variety of interlocking tongue and groove shapes, rounded profiles, shiplap edges, and even work with customers’ specifications for custom-made orders.
Types of Sawmill
- Stationary
- Portable
Depending on the production needs, sawmills can be either stationary or portable. Each type of sawmill is able to accommodate different numbers of operators or workers. Let’s take a look at both!
Stationary Sawmills
Stationary sawmills are large-scale constructions mounted on a foundation in a fixed location. They are often built near water sources to make production easier. Historically, during the industrial revolution, sawmills were powered by steam and therefore required a constant source of water to be able to operate.
Having a water source nearby allowed employees to use the water to transport logs to and from the mill with ease. On top of this, they could prevent the logs from drying out prematurely by storing logs in the river or lake. Modern-day sawmills don’t use steam anymore, however, many sawmills remain in the same location near a water source.
Portable Sawmills
Portable sawmills, otherwise referred to as mobile sawmills, are smaller productions that you may find mounted on a truck or trailer. These sawmills are available in a whole range of sizes, typically designed with specific specifications to suit their purpose and production amounts.
Portable sawmills offer the “portability” that stationary sawmills can’t, they do not require a source of water or a specific amount of land, as they can be moved between sites whenever the operators need to.
Sawmill Blades
Aside from sawmill designs, the types of sawmill can also be categorized by the blade they use. Most modern sawmills will use a combination of blade types, including both:
- Circular blades
- Band saws
Circular Blades
Circular sawmill blades are designed to efficiently perform cross-cuts or buckle logs into any desired length. These blades have additional strength compared to band saws due to their greater thickness, however, the design leads to more kerf waste.
Band Saws
Band saws are excellent for lateral cutting of logs with thinner blades. Their thinner kerfs create less waste during the wood finishing process, thus, improving the sawmill’s efficiency.
With modern-day technology changing saw blade construction, we’re only seeing more and more benefits with every sawmill. Recent developments have provided superior products like Stellite™-tipped blades and tungsten carbide to replace old-fashioned materials, providing longer-lasting and greater efficient blades.
How Are Sawmills Powered?
Once powered by steam, now predominantly powered by electricity. The sawmill’s power source has evolved significantly over the decades, like most technology. The initial mills had waterwheels before windmills came into play. The problem with these systems was that they were subject to changes in the weather. If a water source dried up or the wind stopped blowing, operations came to a halt.
Steam was the primary source of power for sawmills in the 19th century. Sawmills could fuel their steam boilers from the reuse of their wood waste. These boilers powered turbine shafts, which turned the circular and band saw blades to cut the wood.
Electricity replaced steam power in the middle of the 20th century and still to this day continues to be the primary power source in effect. Portable sawmills typically don’t use electric power since the mill sites that use them are usually off the electric grid, therefore, they use diesel and gasoline power sources.
There is currently not a serious shift toward renewable power sources for sawmills since the production process requires vast amounts of energy, but that’s not saying the switch is impossible!
Sawmills also need electric power for other systems like the computers which are used to scan logs and determine the optimal cutting efficiency. These computer systems then send this information to the sawmill components so that they’re able to meet daily requirements.
How Does a Sawmill Work? The Process Lumber Milling
- Felling & Transportation
- Debarking
- Metal Detecting
- Merchandising
- Head Rig Sawing
- Canting
- Resawing
- Edging
- Trimming
- Grading, Drying & Planing
Modern sawmills run largely the same way they have for centuries, only more effectively. The lumber is sent through automated processes at the mill that refine and smooth it until the completed product is produced. Modern sawmills use automation to boost throughput. With the help of this technology, wood from front-end loggers is prepared for the tail-end market on demand.
There are various steps involved in the sawmill lumbering process. Modern sawmills still depend on skilled sawyers, notwithstanding technical developments and the growing use of sophisticated computerization. These employees efficiently steer lumber with their fast movements and keen eyes. The entire sawmill process is described below.
Felling & Transportation
The first stage in getting a log to the sawmill is timber harvesting or logging. Chainsaws are used to fell trees during the forestry process. Felling is the name of this action. Felling basically entails taking the tree down and cutting it to size. The log is then delimbed and put on a truck to be taken to the mill. The logs are unloaded at the mill, arranged into heaps, and then ready for cutting.
Debarking
The logs must be debarked after they arrive at the sawmill. Most sawmills employ machinery such as mechanical ring cutters to remove the bark from each tree. Others make use of water-jet blasters. Sawmills save the bark debris for landscape mulch or to fire the kilns, whichever method they use. A circular saw will buck or cross-cut logs into the proper lengths during the debarking procedure.
Metal Detecting
Standing trees may have imbedded metal from nails or fencing wire that has been concealed by years of growth. Before sawing logs, sawmills must inspect them for metal contamination. Metal pieces that go undetected can destroy blades or send shrapnel flying.
If a log contains metal, it is subjected to a second inspection. Depending on whether the metal can be extracted, the log is either returned to the production line or split into smaller pieces for salvage.
Merchandising
Modern sawmills merchandise logs before sawing them, which is an important step for maximum efficiency. By measuring the length and girth of each raw log, computers estimate the maximum cut value using camera observation or laser scanning. The algorithm then calculates which board, dimensional lumber, and timber sizes the log can supply. The merchandising stage additionally evaluates logs based on standing orders and market conditions.
Head Rig Sawing
Logs are attached to the conveyor and transported to the sawing head rig. Some sawmills have stationary carriages with conveyors that the head rig travels over along with its blades, thus sawing the log lengthwise. Other locations employ a fixed head rig that chops the log as it passes along a movable conveyor. Head rigs are commonly mounted with band saw blades regardless of the method they use. The natural curve of the log is followed by these modern-day, technologically improved head rigs.
Canting
The cants are created as the head rig cuts the log. The first breakdown produces a flat surface on which the head rig can square the workpiece for supplementary cants. This is known as the “best opening face.” Following that, lumber products can be produced from the secondary cants that cut the log into rough sizes. Every leftover slab is recycled into chips, pellets, or mulch.
Resawing
The large cants produced by the head rig are used in the re-sawing process. Several band saw blades were used in this step to cut the cants into smaller pieces in accordance with the specific merchandising instructions. Re-sawing can create a variety of profiles, such as twin or quad bands, horizontal and vertical bands, band center splitters, circle gangs, double arbor gangs, band line bars, and others. Curve sawing is also used in the resaw step to obtain an accurate profile.
Edging and Trimming
The edges of the newly cut timbers, dimensional lumber, and boards are then cut to the appropriate grade size. The products are then fed into a trimmer, which cuts them to the desired lengths. Most sawmills cut wood in 2-foot increments, beginning at 8 feet and increasing to 24 feet or more.
Grading, Drying and Planing
The final step in the process is subjecting the products to quality control. To guarantee that lumber pieces are produced in batches of similar goods, grading is crucial. The lumber is then dried at the sawmill to reduce its naturally high moisture content. In kilns, lumber products are either air-dried or force-dried.
Planers then create the final appearance and size of the product. The products are then stamped with finished grade stamps and packaged for shipment to market.
How to Choose a Sawmill
Choosing the right sawmill is a critical decision that can impact your woodworking projects or lumber business for years to come. By carefully considering your needs, budget, and the features of different sawmills, you can select a model that will serve you efficiently and effectively.
1. Assess Your Needs
- Volume and Frequency: Consider how much lumber you plan to produce and how often you’ll use the sawmill. Larger, more frequent projects may require a more robust and efficient sawmill.
- Type of Wood: The species and size of the logs you plan to mill will influence the power and size of the sawmill you need. Harder woods and larger logs require more powerful sawmills with larger cutting capacities.
- End Use of Lumber: The intended use of the lumber (e.g., furniture making, construction, hobby projects) can also dictate the precision and quality of the sawmill you choose.
2. Choose Between Portable and Stationary Sawmills
- Portable Sawmills: These are ideal if you plan to mill logs in various locations or if you have limited space. They’re easier to move and set up but might have limitations in power and log size capacity.
- Stationary Sawmills: Suited for fixed operations where logs can be brought to the mill. They’re typically more powerful and can handle larger logs and higher volumes of wood.
3. Consider the Power Source
- Gasoline-Powered: Offers portability and power, suitable for remote locations without access to electricity.
- Electric-Powered: Ideal for stationary setups with access to electricity. They’re quieter and usually have lower operating costs but lack the portability of gasoline-powered mills.
4. Look at the Sawing Method
- Band Sawmills: These are popular due to their efficiency, accuracy, and ability to make thinner cuts, which maximizes lumber yield from each log.
- Circular Sawmills: Known for their durability and speed, but they tend to waste more wood due to thicker cuts. They’re often used for larger-scale operations.
5. Determine Your Budget
- Initial Investment: Prices can vary widely based on the size, power, and features of the sawmill. Determine how much you’re willing to invest initially.
- Operating Costs: Consider the long-term costs of running the sawmill, including fuel, maintenance, blade replacement, and any necessary upgrades.
6. Evaluate Features and Accessories
- Cutting Capacity: Ensure the sawmill can handle the length and diameter of the logs you plan to mill.
- Adjustability and Ease of Use: Look for features that allow for easy adjustments to cut different sizes of lumber and features that simplify the milling process.
- Safety Features: Consider sawmills with built-in safety features to protect the operator.
- Support and Warranty: Good customer support and a solid warranty can be invaluable, especially for first-time sawmill operators.
7. Read Reviews and Seek Recommendations
- Look for reviews from current sawmill users to get insights into the reliability, performance, and customer service associated with different brands and models.
- Seeking recommendations from experienced users or joining woodworking forums can also provide valuable firsthand information.
How to Use a Sawmill
Whether you’re working with a portable or stationary sawmill, the basic principles are similar.
Here’s a general guide on how to use a sawmill:
1. Safety First
- Before starting, ensure you have the appropriate safety gear, including gloves, eye protection, ear protection, and sturdy footwear.
- Familiarize yourself with the sawmill’s operating manual and safety features.
2. Prepare the Work Area
- For stationary sawmills, ensure the area around the mill is clear of debris and obstacles.
- For portable sawmills, set up the mill on a level, stable surface, and secure it according to the manufacturer’s instructions.
3. Log Preparation
- Remove any dirt, stones, or metal (such as nails or fencing) from the logs to prevent damage to the sawmill blades.
- If necessary, trim the log to fit the sawmill’s capacity, ensuring it’s as straight as possible for even milling.
4. Loading the Log
- Use the sawmill’s loading system (which may be manual, semi-automatic, or fully automatic) to safely load the log onto the sawmill bed.
- Secure the log according to the sawmill’s guidelines, ensuring it’s stable and aligned for the first cut.
5. Setting the Cut
- Determine the desired thickness for your first cut, considering any adjustments for the blade width to maximize lumber yield.
- Adjust the sawmill’s head height and position to align the blade with your marked cut line or desired starting point.
6. Making the First Cut
- Start the sawmill according to the manufacturer’s instructions, allowing the blade to reach full speed before beginning the cut.
- Feed the sawmill head through the log at a consistent speed, ensuring a smooth and even cut. The speed may vary based on the wood species and sawmill type.
7. Rotating and Cutting the Log
- After the first cut, rotate the log to the next side to square it off, securing it in place before each cut.
- Continue making cuts, adjusting the head height as needed to achieve the desired lumber dimensions.
8. Final Cuts and Lumber Removal
- Once the log is squared and you’ve cut the desired boards, turn off the sawmill and remove the lumber.
- Stack the lumber properly for drying, using stickers (spacers) between the boards to allow for air circulation.
9. Maintenance and Cleanup
- After use, clean the sawmill to remove sawdust and debris, paying particular attention to the blade and moving parts.
- Perform regular maintenance checks as recommended by the manufacturer, including blade sharpening and replacement, lubrication, and adjustments.
Tips for Efficient Sawmill Use
- Plan Your Cuts: Before you start, plan your cuts to maximize the lumber yield from each log.
- Stay Organized: Keep the work area clean and organized to improve efficiency and safety.
- Learn and Adapt: Experience will improve your efficiency and the quality of your lumber. Take notes on what works well and adjust your techniques as needed.
Other guides for tool use:
FAQs (Frequently Asked Questions)
What’s the difference between a lumber mill and a sawmill?
The sawmill includes all the land on which the sawmill sits, along with being a machine used for cutting (milling) lumber. A lumber mill is basically the same, as is often referred to as a sawmill, a large manufacturing plant to a small, simple, hand-operated machine with a blade that can cut long sections of wood and plane them into flat pieces.
How does a sawmill work?
With the aid of large bandsaw blades, a sawmill produces lumber from logs. To produce huge amounts of rough-cut lumber, the same procedure is carried out log by log, repeatedly.
What’s meaning of saw mill?
The entire parcel of land on which the sawmill is situated, including the log-sorting yard, all milling equipment, and the storage area for wooden planks, is referred to as the sawmill. This means that the sawmill is seen as the entire process of turning wood into lumber, timber, or board.
How did old sawmills work?
Early sawmills simply converted the whipsaw to mechanical power, usually powered by a water wheel to speed up the process. By means of a connecting rod known as a pitman arm, the circular motion of the wheel was transformed into a back-and-forth motion of the saw blade. Historically, sawmills operated on steam power during the industrial revolution and needed a steady supply of water to function.