For optimal performance, safety, and the achievement of your goals, choosing the appropriate blade for your sawmill is essential. Additionally, in order to prevent blade damage, it’s critical to select the proper cutting tool for your machine.
Before you go shopping for a sawmill blade, you should know what to look for and what kind of wood you intend to cut. In this article, we’ll cover the components of sawmill blades, factors to consider when choosing a blade, and how much you should budget for a new sawing tool.
Table of Contents
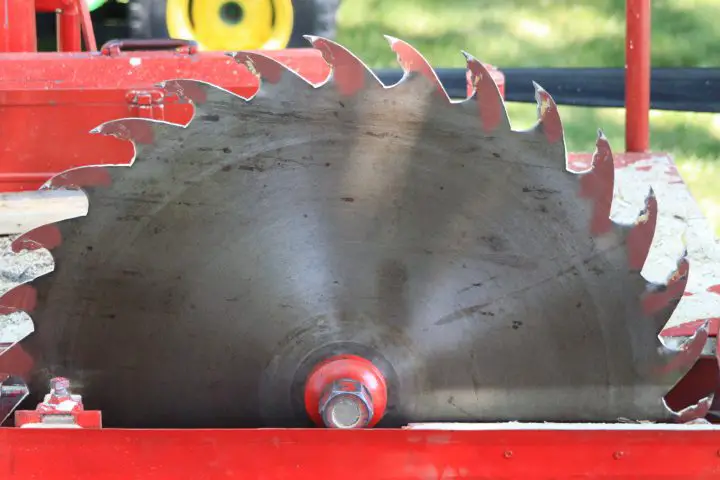
Sawmill Blade Parts
Sawmill blades come in a variety of designs, thicknesses, and widths. It is beneficial to understand the various blade parts and terms in order to understand how they function before selecting a blade for an industrial sawmill.
Here are the parts and terms you can expect to find in a typical sawmill blade:
- Teeth
- Tooth pitch
- Tooth angle
- Tooth type
- Gullet
- Gullet depth
- Blade width
- Blade type
- Tipping
Teeth
All blades have teeth that act like knives, cutting and releasing wood at the same time. A blade with more teeth will typically produce a smoother cut than a blade with fewer teeth. Although they cut smoother, they will typically cut slower than blades that have fewer teeth.
Tooth Pitch
The distance between the tooth tips is known as the “tooth pitch.” Each tooth loses strength as the teeth are spaced closer together. For longer, faster-moving blades, a wider tooth pitch is used. When choosing a blade, take into account the tooth pitch to make sure it is powerful enough to cut through the material you have chosen.
Tooth Angle
The tooth angle calculates how far forward a tooth is tilted in relation to the blade’s center. When selecting a tooth angle, take into account the material you intend to cut.
Typically, a high hook angle is needed for a dense, sturdy wood. High hook angles, which function more like a chisel, are also preferred for rip-cutting and resawing. Low hook angles are typically preferred for cross-cutting because they perform tasks more like a scraper than a chisel.
Tooth Type
The most important factor to take into account when you want a high-quality cut is tooth type. There are typically four different tooth types:
- Hook
- Skip
- Rounded
- Standard or raker
Equally spaced standard teeth are advised for general use. This kind of tooth is frequently employed in narrow band saw blades. Wide blades frequently have rounded teeth, which are very strong at the points.
Hook teeth are ideal for quick rip-cutting because they have wide round or flat gullets. Skip teeth have flat, wide gullets and are much less aggressive than hook teeth, making them the best choice when it comes to cutting thick or undried wood.
Gullet
The area between the teeth that is rounded is known as the gullet. As a blade passes through a workpiece, gullets collect sawdust.
Gullet Depth
The distance between the gullet’s lowest point and its tooth tip is known as gullet depth. Deeper gullets are found in blades made for softwoods like pine or balsam, whereas shallower gullets are found in blades made for hardwoods like ash and hickory.
A larger chip results from a deeper gullet. Selecting a gullet size that is deep enough for the cut is crucial. Larger gullets are required for a bigger logs. A gullet that is too tiny slows the bite and increases the risk of the blade wandering or overheating.
Blade Width
The breadth of a blade is the separation between its body and its tooth tips. Wide blades are made for sawmills with high horsepower and a rapid feed rate. For low horsepower sawmills, narrow blades are constructed. Although a band saw will have requirements for blade width, in general, straighter cuts result with broader blades.
Blade Metal
There are numerous blade materials available from which to pick. The lifespan of the blade is influenced by the type of metal chosen. The most typical metal used to make sawmill blades is carbon steel, which works well for high production rates.
To increase a blade’s toughness and durability, other metals may be added to the mix. The blade metal must be both flexible and hard in any case. A band saw blade’s flexibility allows it to move as a band, while its hardness gives the teeth the power to cut.
Tipping
A finished swage or teeth with a Stellite tip may be present on a blade. Blades with a Stellite tip are perfect for heavy-duty cutting and help save downtime because they are able to maintain their sharpness. Both carbide and chromium are also strong materials for tips.
Choosing Sawmill Blades
Sawmill blade selection demands serious thought. The incorrect cutting tool for your machinery can lead to a number of problems, such as delayed production and blade damage. When choosing the ideal blade for your sawmill, you need to consider a number of things, such as:
- What materials you will be cutting
- If you require slower or faster feed rates
- How essential smooth cuts are
- If both speed and smoothness are necessary
- The blade’s thickness and quality will determine how wide the kerf is
- Exactly what kind of cuts the blade will make
- The sawmill’s power
- Blade recommendations from the sawmill’s manufacturer
For the majority of industrial sawmills, tooth requirements are crucial. Depending on the power and type of lumber—hardwood or softwood—certain teeth are best. Let’s take a look at circular vs. bandsaw blades.
Circular vs Bandsaw Blades
Circular saws and band saws can both be used in some industrial sawmills. If you are required to pick between either one, think about which one is more crucial for your company’s success: production speed or kerf size. In summary, band saw blades create the least amount of kerf, while circular blades are preferred for quick cutting.
To assist you in selecting the best blade for your mill, we’ll discuss the advantages and disadvantages of both designs.
Circular Saw Blades
Blades for circular saw machines are thicker than those for band saws, such as those with carbide tips. A high feed rate, little blade vibration, and smooth cuts are all characteristics of carbide-tipped blades.
Wherever speed, quality, and accuracy are required, circular saw machines with carbide-tipped blades are a great solution. They also produce a useful saw for cutting substantially sized beams. Band saw mills often need more maintenance, but circular blade mills may process twice as much lumber.
Circular saw blades come in a variety of tooth counts and spacings. Every tooth on a conventional circular saw is separated by the same amount of space. Circular saw blades with variable pitch (VPD) have different tooth spacing between each tooth. Vibrations are lessened due to this variable pitch design.
Bandsaw Blades
The blade of a band saw machine is a thin, continuous strip of steel. They create less kerf loss and use less energy than circular sawmills. If high productivity is not a necessity, band saws are a more affordable and adaptable solution.
With a band saw blade with a kerf of roughly 3/32 inch as opposed to 1/4 inch, you can extract up to 20% more lumber from a log than you would with a circular blade. The versatility of a band saw allows you to create whatever product you desire for customers by cutting smooth, unique forms.
Industrial sawmilling makes use of wide band saw blades. Large steel belts that may measure 14 inches in width make up modern wide band saw blades. Cutting through massive logs that are too big for circular saws, by moving over pulleys. Wide band saw blades are produced to meet the output requirements of an industrial sawmill. Wide band saw blades come in a variety of varieties, including blades with Stellite tips, which are excellent for use with hardwoods.
For large sawmills to efficiently manufacture high-quality lumber, stationary band saw equipment is needed. The most common tools for sawing logs are band saws. Even though circular saws cut faster, a band saw mill often produces a better yield of board feet than a circular mill.
Related: What is Sawmill
Softwood vs. Hardwood
You would assume that a hardwood tree would be more challenging to chop than a softwood when you hear the terms “hardwood” and “softwood.” While this is frequently the case, hardwood does not imply that a block of wood is inherently stronger or harder than a softwood.
Conifers, such as pine, fir, and spruce, which contain needles, are typically referred to as softwoods. Softwoods often cost less than hardwoods because they grow more quickly.
Hardwoods shed their leaves at the conclusion of the growth season since they are deciduous trees. Since hardwoods are often more dense than softwoods, they might be harder to saw, demand more work, and take longer to complete. In addition to growing more slowly than softwoods, hardwoods are more expensive. This kind of wood is preferred for making elegant furniture and exquisite flooring since it is valued for both its durability and its range of hues and patterns.
It is important to think about the species of the tree before feeding it into a sawmill because they can differ so much, even though there are other factors to take into account when selecting a cutting method. A blade may become damaged if the tree and the blade are not compatible.
When selecting a blade for cutting hardwood or softwood, take the tooth design into account. For instance, Stellite, or carbide-tipped blades, should be used to cut tough exotic wood since they maintain their sharpness longer. Think about your gullet and your tooth pitch and height as well. A too-narrow gullet might lead to issues like overheating or saw fractures.
Learn more about softwood and hardwood here!
Cost
Depending on length, width, tooth pattern, tipping, and other criteria, band saw blades with widths ranging from 4 to 14 inches can cost anywhere between $300 and $1,600.
The price of circular blades, which typically ranges from $100 to $300 and comes in sizes ranging from 14 inches to 30 inches, will also vary depending on the tooth design, tipping, shipping, and other factors.
FAQs (Frequently Asked Questions)
What is the best blade for a sawmill?
This depends on whether your priority is production speed or kerf size. Bandsaws are best if you wish to create the least amount of kerf, while circular blades are best for quick cutting.
How long does a sawmill blade last?
On average your sawmill blade should last 6 months to as long as a few years depending on what you’re cutting with it. This can be easily affected by how dirty the logs are, along with the size and other factors.
How many times can you sharpen a sawmill blade?
You should be able to sharpen your sawmill blade two or three times before being required to replace it. However, premature breakage can occur as a result of a variety of scenarios, which would lead you to replacing your blade sooner.
What is the pitch of a sawmill blade?
The pitch of a sawmill blade is the distance between the tips of the teeth on the blade. Therefore, the pitch is able to determine the cutting power each tooth has and how rough the blade will cut.